Introduction
In the world of optical systems, coatings play a vital role in enhancing the performance and efficiency of devices. Among the various types of coatings available, dielectric and metallic optical coatings are two prominent categories. In this comprehensive guide, we will delve into the details of both these coatings, comparing their characteristics, advantages, applications, and more.
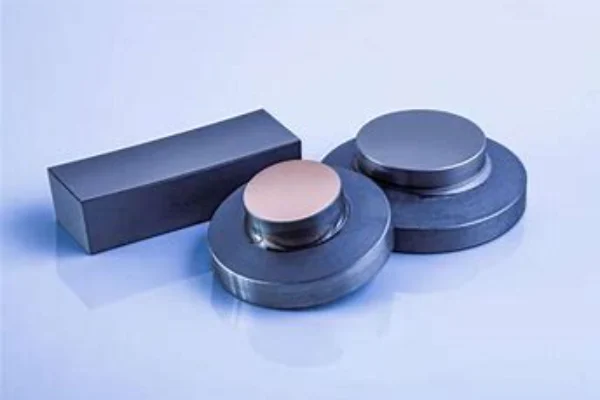
Understanding Optical Coatings
Optical coatings are integral to the performance and functionality of various optical systems, and among them, dielectric and metallic coatings stand out for their unique properties and applications. Dielectric coatings are constructed from multiple layers of dielectric materials, designed to reflect specific wavelengths of light while transmitting others. This selective reflection and transmission make them highly suitable for applications requiring precision control over optical properties.
One of the key characteristics of dielectric coatings is their high reflectivity for specific wavelengths, allowing them to be used in applications where precise control over reflection is needed. Moreover, they are known for their durability and long-lasting performance, making them a reliable choice for long-term applications. Customization is another strong point of dielectric coatings, as they can be tailored to meet the specific requirements of different applications, providing flexibility and adaptability.
On the other hand, metallic coatings are made from metals like aluminum, gold, or silver, and they are known for their wide spectral range and versatility. Unlike dielectric coatings, which are selective in their reflection and transmission, metallic coatings work across a broad range of wavelengths, making them suitable for applications requiring a wide spectral response. This broad spectral range is one of the defining characteristics of metallic coatings, and it allows them to be used in various applications, including mirrors and filters, where a wide range of wavelengths needs to be handled.
Flexibility is another key feature of metallic coatings, as they can be adapted to different applications with ease, providing a versatile solution for various optical needs. Cost-effectiveness is also an important consideration, and metallic coatings are generally more affordable than dielectric coatings, making them an economical choice for many applications.
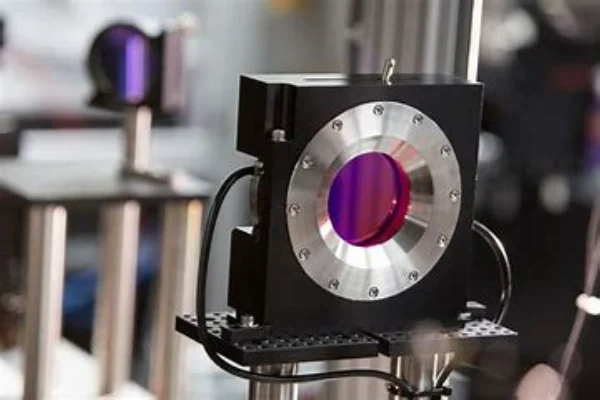
The comparison between dielectric and metallic coatings reveals distinct advantages and characteristics that make each suitable for specific applications. Dielectric coatings, with their high reflectivity, durability, and customization, are ideal for applications requiring precision and control over optical properties. Their ability to reflect specific wavelengths while transmitting others allows them to be used in applications like laser systems, where precise control over beam characteristics is essential. Metallic coatings, with their broad spectral range, flexibility, and cost-effectiveness, are suitable for a wide array of applications, including telescopes and sensors, where a wide spectral response is needed. Their versatility and affordability make them a popular choice for various optical needs.
In conclusion, both dielectric and metallic coatings have unique characteristics and advantages that make them valuable in the field of optics. Dielectric coatings, with their precision control, thermal stability, and low absorption, offer efficiency and reliability for specific applications. Metallic coatings, with their versatility, ease of production, and economical nature, provide a wide range of solutions for different optical needs.
The choice between these two types of coatings depends on the specific requirements of the application, and understanding their unique properties can help in making an informed decision that best suits the needs of the optical system. Whether it’s the precision and control offered by dielectric coatings or the versatility and cost-effectiveness of metallic coatings, both have a significant role to play in enhancing the performance and efficiency of optical devices.
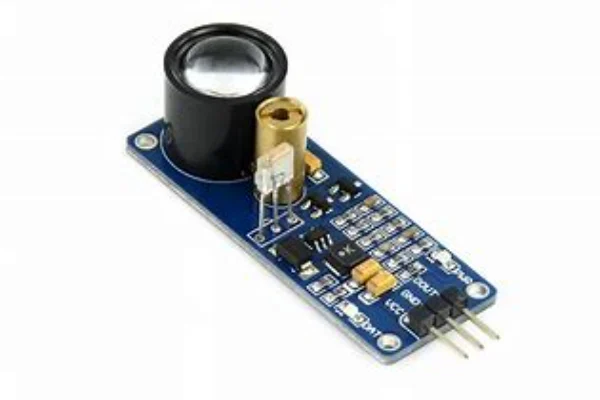
Comparative Analysis: Dielectric vs. Metallic Optical Coatings
In the realm of optical coatings, a comparative analysis between dielectric and metallic optical coatings reveals distinct characteristics and advantages that cater to different needs and applications. Understanding these differences is crucial for selecting the right coating for a specific optical system.
Dielectric coatings are renowned for their precision control, thermal stability, and low absorption. These attributes make them highly desirable in various optical applications. The precision control in dielectric coatings is achieved through the careful design and layering of dielectric materials, allowing them to reflect specific wavelengths of light while transmitting others.
This ability to selectively control reflection and transmission is vital in applications where exact optical properties are required. For example, in laser systems, dielectric coatings can be used to control beam characteristics, ensuring that the laser operates at the desired wavelength and intensity. The precision control also extends to the customization of dielectric coatings, where they can be tailored to meet the specific requirements of different applications, providing flexibility and adaptability.
Thermal stability is another significant advantage of dielectric coatings. They exhibit excellent stability under varying temperature conditions, making them suitable for applications where temperature fluctuations are common. This thermal stability ensures that the optical properties of the coating remain consistent, even when exposed to changes in temperature. In high-power laser systems, for example, dielectric coatings must withstand intense heat generated by the laser, and their thermal stability ensures that they continue to perform efficiently without degradation.
The low absorption of dielectric coatings further enhances their performance by minimizing the absorption of light. This ensures that the majority of the light is either reflected or transmitted, depending on the design of the coating, leading to efficient performance. Low absorption is particularly important in applications where energy efficiency is a priority, as it ensures that minimal energy is lost in the form of absorbed light.
On the other side of the spectrum, metallic coatings offer versatility, ease of production, and economical advantages. The versatility of metallic coatings stems from their ability to work across a broad range of wavelengths. Unlike dielectric coatings, which are selective in their reflection and transmission, metallic coatings can be used in various applications, including mirrors and filters, where a wide range of wavelengths needs to be handled.
This broad spectral range allows metallic coatings to be used in diverse optical applications, from telescopes to sensors, providing a one-size-fits-all solution for various optical needs.
Ease of production is another strong point of metallic coatings. They are generally easier and quicker to manufacture compared to dielectric coatings. This ease of production translates into faster turnaround times and the ability to produce large quantities of coatings in a shorter period. In industries where time is of the essence, the ease of production of metallic coatings can be a significant advantage. Moreover, the manufacturing process of metallic coatings often involves well-established techniques like physical vapor deposition (PVD) or sputtering, which are widely used and understood in the industry.
Economical considerations are also paramount when choosing between dielectric and metallic coatings. Metallic coatings are often more cost-effective than dielectric coatings, making them an attractive option for applications where budget constraints are a concern. The cost-effectiveness of metallic coatings is achieved through their ease of production and the use of commonly available materials like aluminum, gold, or silver. This affordability does not compromise their quality or performance, as metallic coatings continue to provide reliable and versatile solutions for various optical needs.
In conclusion, the comparison between dielectric and metallic optical coatings reveals a complex interplay of characteristics and advantages that cater to different needs and applications. Dielectric coatings, with their precision control, thermal stability, and low absorption, offer specialized solutions for applications requiring exact optical properties. Metallic coatings, with their versatility, ease of production, and cost-effectiveness, provide a broader range of solutions that can be adapted to various optical needs.
The choice between these two types of coatings is not a simple one-size-fits-all decision but requires a careful understanding of the specific requirements of the application. Whether it’s the specialized performance of dielectric coatings or the broad applicability of metallic coatings, both have a significant role to play in the field of optics. By recognizing their unique properties and advantages, one can make an informed decision that best suits the needs of the optical system, enhancing performance, efficiency, and overall functionality.
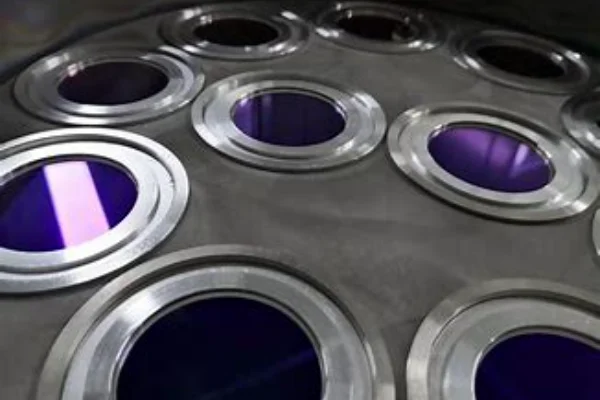
Applications in Optical Systems
In the field of optical systems, both dielectric and metallic coatings find essential applications, each serving specific purposes. Dielectric coatings are prominently used in laser systems, where they play a crucial role in controlling beam characteristics. By reflecting specific wavelengths and transmitting others, they ensure that lasers operate with desired precision and efficiency. Additionally, dielectric coatings are vital in the telecommunication industry, particularly in fiber optics, where they facilitate accurate signal transmission.
On the other hand, metallic coatings find extensive use in telescopes, where they enhance imaging by working across a broad spectral range. Their versatility also extends to various sensors, where metallic coatings are employed for accurate detection and measurement. Whether it’s the precision control offered by dielectric coatings or the wide applicability of metallic coatings, both contribute significantly to the advancement and efficiency of modern optical systems. Their unique characteristics and applications underline the importance of understanding the specific needs of an optical system to choose the appropriate coating.
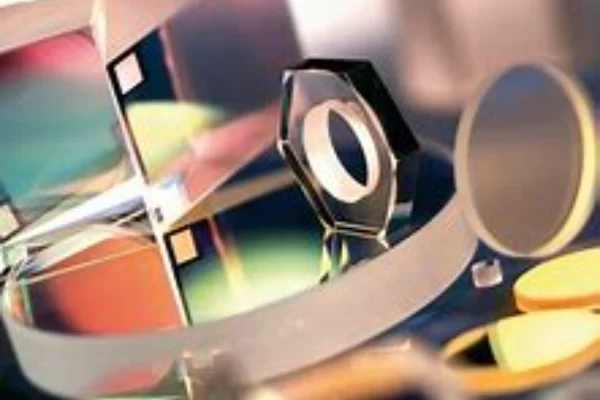
Conclusion
The choice between dielectric and metallic optical coatings depends on the specific requirements of the application. While dielectric coatings offer precision and efficiency, metallic coatings provide versatility and cost-effectiveness. By understanding the unique characteristics of each, one can make an informed decision that best suits the needs of the optical system.
FAQs
- What materials are commonly used in dielectric coatings?
- Dielectric coatings often use materials like titanium dioxide, silicon dioxide, etc.
- How are metallic coatings applied to the surface?
- Metallic coatings are typically applied through physical vapor deposition (PVD) or sputtering.
- Can dielectric coatings be used in high-power laser systems?
- Yes, dielectric coatings are suitable for high-power laser systems due to their thermal stability.
- What are the environmental considerations for metallic coatings?
- Metallic coatings may require special handling and disposal due to the metals involved.
- Which coating is better for a broad spectral range?
- Metallic coatings are generally preferred for applications requiring a broad spectral range.
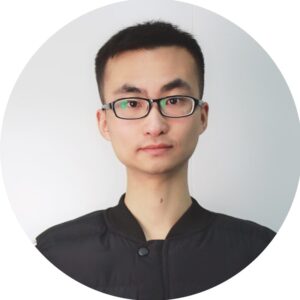
Frank
Frank graduated from the University of Shanghai for Science and Technology, majoring in optics. As a technical engineer at Crylink Company, he deeply understands crystal materials and laser components.
Related Video(s) with this Article
Related Product(s) with this Article
Related Application(s) with this Article