Introduction
Optical coatings play a pivotal role in the performance of optical systems. They are used to control the reflection, transmission, and absorption of light. The three main types of optical coatings are dielectric, metallic, and hybrid coatings. Each type has its unique characteristics, advantages, and disadvantages. In this article, we delve into the specifics of these coatings and compare their suitability for different crystal materials.
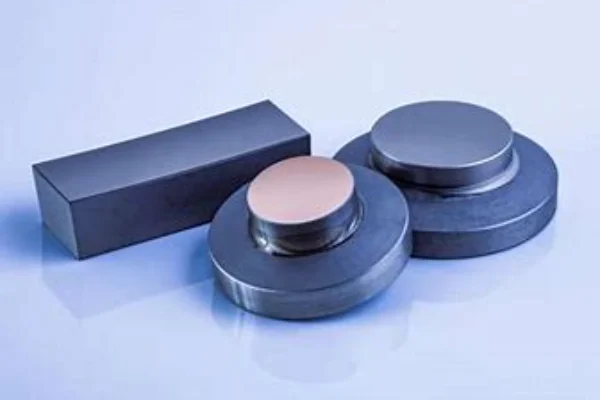
Dielectric Coatings
Dielectric coatings, a cornerstone in the field of optics, are composed of multiple thin layers of dielectric materials. These materials, characterized by their inability to conduct electricity, have found a significant place in the realm of optics due to their unique properties that allow them to manipulate light in various ways. They can reflect, transmit, or filter light, making them a versatile tool in optical applications.
One of the key advantages of dielectric coatings is their high reflectivity. In optical systems, the loss of light can lead to a decrease in system efficiency, making high reflectivity a sought-after property. Dielectric coatings, with their ability to offer high reflectivity, are therefore ideal for applications that require minimal light loss. This high reflectivity is not just across a broad spectrum, but can be designed to reflect specific wavelengths of light. This property is particularly beneficial in laser technology, where controlling the wavelength of light is crucial.
In addition to their high reflectivity, dielectric coatings are also known for their durability. They are highly resistant to damage, which makes them suitable for applications that involve high power densities. In such applications, other types of coatings might degrade or fail, but dielectric coatings can withstand these harsh conditions, providing reliable performance over extended periods.
However, despite these advantages, dielectric coatings are not without their drawbacks. One of the main disadvantages of dielectric coatings is their sensitivity to the angle of incidence and polarization of light. The angle of incidence refers to the angle at which light strikes the surface of the coating, while polarization refers to the orientation of the light waves.
Changes in these parameters can significantly affect the performance of the dielectric coating. For instance, a change in the angle of incidence can alter the amount of light that is reflected, while a change in polarization can affect the phase of the reflected light. This sensitivity can limit the effectiveness of dielectric coatings in applications where the angle of incidence or polarization cannot be tightly controlled.
Another challenge with dielectric coatings is their manufacturing process. Creating a dielectric coating involves depositing multiple thin layers of dielectric material onto a substrate. This process requires precise control over the thickness and uniformity of each layer, which can be difficult to achieve. Furthermore, the process is time-consuming and can require specialized equipment, which can increase the cost of the coating. Despite these challenges, the unique properties of dielectric coatings make them a valuable tool in the field of optics. They continue to be used in a wide range of applications, from laser technology to telecommunications, and ongoing research is aimed at further improving their performance and reducing their cost.
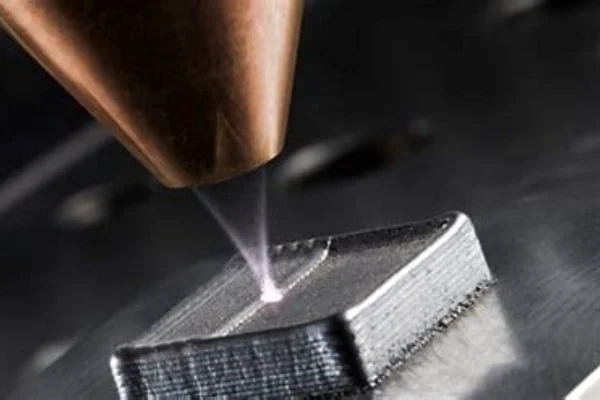
Metallic Coatings
Metallic coatings, as the name suggests, utilize metals such as aluminum, silver, or gold to manipulate light. These coatings are a fundamental component in a variety of optical applications, including mirrors, reflectors, and shielding applications. The metals used in these coatings have been carefully selected for their unique optical properties, particularly their ability to reflect light.
One of the primary advantages of metallic coatings is their broad bandwidth reflectivity. Unlike other types of coatings, which may only reflect specific wavelengths of light, metallic coatings can reflect a wide range of wavelengths. This makes them incredibly versatile, as they can be used in a variety of applications, from visible light mirrors to infrared reflectors. This broad bandwidth reflectivity is a unique characteristic of metallic coatings and is one of the reasons they are so widely used in optical applications.
In addition to their broad bandwidth reflectivity, metallic coatings are also less sensitive to the angle of incidence and polarization of light compared to dielectric coatings. This means that the performance of metallic coatings is more stable and predictable, even when the angle at which light strikes the coating or the orientation of the light waves changes. This stability can be a significant advantage in applications where these parameters cannot be tightly controlled.
However, despite these advantages, metallic coatings also have their drawbacks. One of the main disadvantages of metallic coatings is their lower reflectivity compared to dielectric coatings. While metallic coatings can reflect a wide range of wavelengths, the amount of light they reflect is typically less than that of dielectric coatings. This lower reflectivity can limit the effectiveness of metallic coatings in applications that require high reflectivity, such as laser technology.
Another challenge with metallic coatings is their susceptibility to tarnishing and corrosion. Metals like silver and gold, while excellent reflectors of light, can tarnish over time when exposed to certain environmental conditions. This tarnishing can degrade the performance of the coating, reducing its reflectivity and potentially leading to system failure. Similarly, metals can also corrode when exposed to certain chemicals, which can further degrade the performance of the coating.
Despite these challenges, metallic coatings continue to be a valuable tool in the field of optics. Their broad bandwidth reflectivity and stability make them suitable for a wide range of applications, and ongoing research is aimed at improving their reflectivity and resistance to tarnishing and corrosion. By understanding the advantages and disadvantages of metallic coatings, one can make informed decisions when designing and manufacturing optical systems.
Hybrid Coatings
Hybrid coatings represent a fusion of the properties of dielectric and metallic coatings, designed to harness the strengths of both types while mitigating their weaknesses. These coatings are engineered to offer high reflectivity across a broad range of wavelengths, similar to metallic coatings, while also maintaining the high damage threshold characteristic of dielectric coatings. This makes them less sensitive to changes in the angle of incidence and polarization of light, enhancing their performance stability in various applications. Moreover, hybrid coatings boast enhanced durability and resistance to damage compared to purely metallic or dielectric coatings, making them a robust choice for demanding optical applications.
However, the main challenge with hybrid coatings lies in their complexity. The process of designing and manufacturing these coatings involves a careful balance of the properties of dielectric and metallic materials, which can be challenging and costly. Despite this, the superior performance characteristics of hybrid coatings often justify the additional investment, making them a valuable tool in the field of optics.
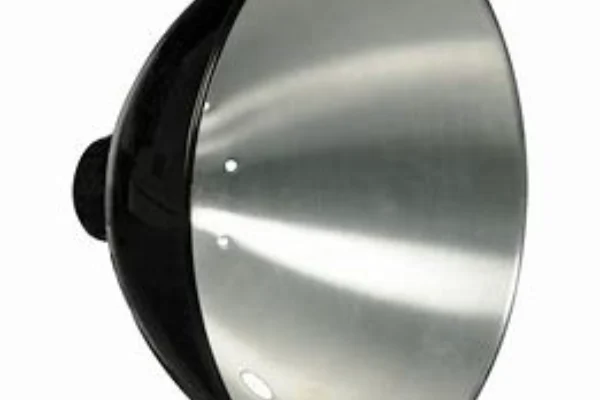
Comparing Evaporation and Sputtering Coating Techniques
Evaporation and sputtering are two prevalent techniques in the application of optical coatings, each offering unique advantages and presenting certain challenges. Evaporation, a process that involves heating the coating material until it transforms into vapor and then allowing it to condense on the substrate, is valued for its simplicity and cost-effectiveness. This technique is versatile, accommodating a wide range of materials, including those that are sensitive to high temperatures. However, evaporation does have its limitations. It can potentially result in non-uniform coatings, which may not meet the stringent requirements of certain optical applications. Additionally, it is less suitable for materials with high melting points, limiting its applicability in some scenarios.
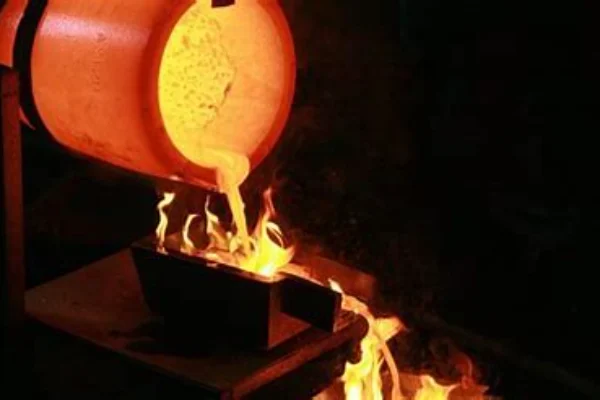
On the other hand, the sputtering technique, which involves bombarding the coating material with ions and allowing the ejected atoms to deposit on the substrate, is renowned for producing highly uniform and dense coatings. This precision makes it particularly suitable for high melting point materials, expanding its utility in the field of optical coatings. However, sputtering is not without its challenges. It is a complex process that requires a high level of expertise and sophisticated equipment, which can drive up costs. Furthermore, it necessitates a high vacuum environment, which can limit its applicability in certain settings.
Therefore, the choice between evaporation and sputtering is not a one-size-fits-all decision. It depends largely on the specific requirements of the optical coating application, the properties of the crystal material, and the resources available for the coating process. By understanding these techniques and their respective strengths and weaknesses, one can make an informed decision that best suits their specific needs and constraints in the realm of optical coatings.
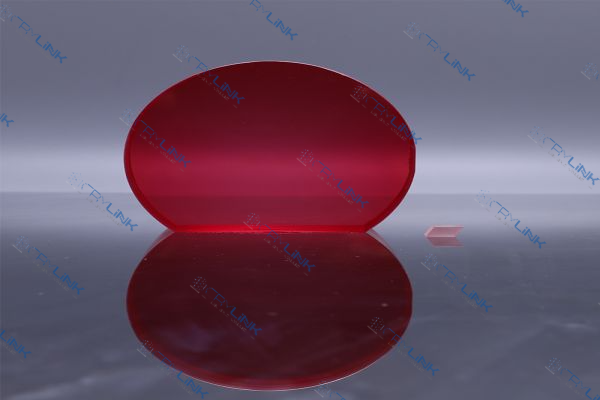
Conclusion
Dielectric, metallic, and hybrid coatings each have their unique advantages and disadvantages. The choice between them depends on the specific requirements of the optical system. Similarly, the choice between evaporation and sputtering depends on the properties of the crystal material and the desired characteristics of the coating. By understanding these factors, one can make informed decisions when designing and manufacturing optical systems.
FAQs
- What are the main types of optical coatings?
The main types of optical coatings are dielectric, metallic, and hybrid coatings. - What are the advantages of dielectric coatings?
Dielectric coatings offer high reflectivity and are highly resistant to damage. - What are the disadvantages of metallic coatings?
Metallic coatings have lower reflectivity than dielectric coatings and can be prone to tarnishing and corrosion. - What is the difference between evaporation and sputtering coating techniques?
Evaporation involves heating the coating material until it vaporizes, while sputtering involves bombarding the coating material with ions. - Which coating technique is suitable for high melting point materials?
Sputtering is more suitable for high melting point materials compared to evaporation.
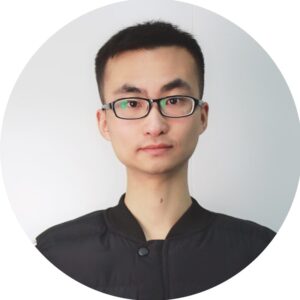
Frank
Frank graduated from the University of Shanghai for Science and Technology, majoring in optics. As a technical engineer at Crylink Company, he deeply understands crystal materials and laser components.
Related Video(s) with this Article
Related Product(s) with this Article
Related Application(s) with this Article