Introduction: Understanding Optical Coatings
In the world of optics, optical coatings play a pivotal role. These coatings are thin layers of material deposited on optical components such as lenses and mirrors. They are essential in controlling the reflection, transmission, and absorption of light. This article will delve into the principles of thin film deposition and explore the significance of optical coatings in various applications.
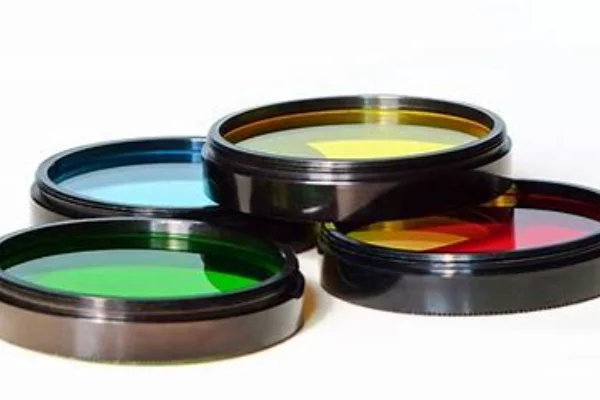
The Science Behind Optical Coatings
Optical coatings are specialized layers applied to the surface of optical elements, designed to enhance or minimize certain properties of light as it interacts with the surface. These coatings are more than just superficial treatments; they are a complex fusion of science and engineering that plays a crucial role in modern optics.
The process of creating optical coatings is known as thin film deposition, where materials are deposited in layers that are only a few atoms thick. This intricate process requires a deep understanding of materials science and the behavior of light. There are two main methods used in thin film deposition: Physical Vapor Deposition (PVD) and Chemical Vapor Deposition (CVD).
Physical Vapor Deposition, or PVD, involves physically moving material from a source to the substrate. It’s a process that can be likened to painting a surface, where the material is transferred and adheres to the substrate in a controlled manner. PVD is commonly used in various industries, including electronics, automotive, and aerospace, for its ability to create uniform and high-quality coatings.
Chemical Vapor Deposition, or CVD, on the other hand, involves chemically reacting materials to form a thin film on the substrate. Unlike PVD, where the material is physically transferred, CVD creates the coating through a chemical reaction. This method allows for more complex coatings and is often used in semiconductor manufacturing and other high-tech applications.
The choice between PVD and CVD depends on the specific requirements of the optical component and the desired properties of the coating. Both methods have their advantages and challenges, and the selection often involves a careful consideration of factors such as material compatibility, thickness, uniformity, and environmental considerations.
In conclusion, optical coatings are an essential aspect of modern optics, providing the means to control and manipulate light in ways that were previously impossible. The principles of thin film deposition, including the methods of PVD and CVD, are at the core of this technology. They represent a fascinating intersection of physics, chemistry, and engineering, enabling innovations that continue to shape our world. Whether in the lenses of our eyeglasses or the advanced components of space telescopes, optical coatings are a testament to human ingenuity and the relentless pursuit of knowledge and perfection.
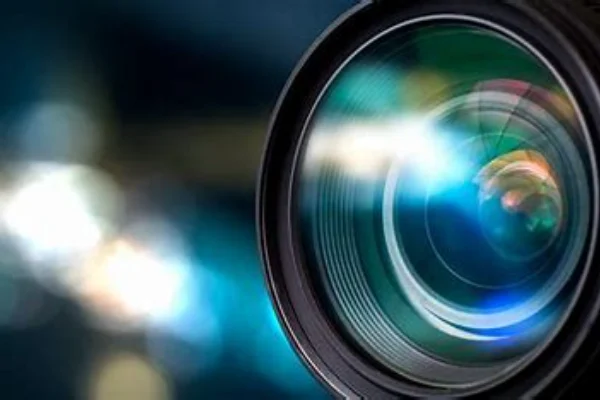
Applications of Optical Coatings
Optical coatings are not merely a technological curiosity; they are a vital part of many applications that touch our daily lives. From the eyeglasses we wear to the cameras we use, these coatings play a pivotal role in enhancing optical performance and ensuring the durability of optical components.
The primary application of optical coatings is in enhancing the performance of lenses, mirrors, and other optical components. By carefully selecting the materials and methods of deposition, these coatings can increase transmission, reduce reflection, and control polarization. For example, anti-reflective coatings on eyeglass lenses reduce glare and reflections, allowing for clearer vision. In telescopes and microscopes, coatings can increase the amount of light that passes through the lenses, enabling clearer and brighter images.
But the applications of optical coatings go beyond just enhancing performance. They also provide protection and durability to optical components. Environmental factors such as moisture, dust, and abrasion can degrade the quality of optical elements over time. Coatings act as a shield, protecting the underlying material from these factors. For instance, coatings on camera lenses protect against scratches and smudges, ensuring that the lens continues to provide clear images over time.
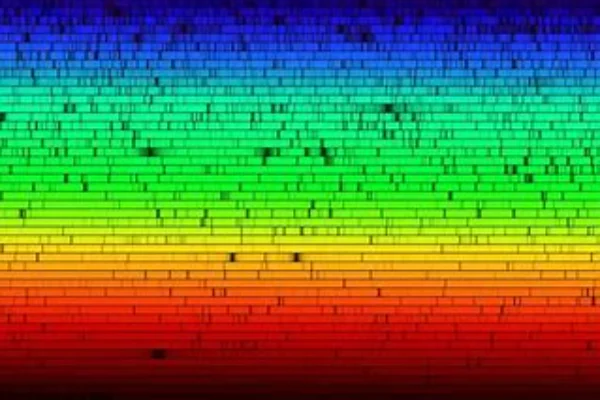
The science behind these applications is complex and requires a deep understanding of the properties of light and materials. Different applications require different types of coatings, and the choice of materials and deposition methods must be carefully tailored to the specific needs of the application. The development of new coatings and deposition techniques continues to be an area of active research and innovation, driven by the ever-increasing demands of modern technology.
In the world of optics, the importance of coatings cannot be overstated. They are a subtle yet powerful tool that enables us to see the world more clearly and protect the delicate optical components that make this possible. From enhancing the performance of everyday objects like eyeglasses and cameras to ensuring the longevity of specialized equipment in scientific and industrial settings, optical coatings are a testament to the ingenuity and creativity of scientists and engineers. Their continued development promises to unlock even more possibilities, pushing the boundaries of what is possible with light and optics.
Types of Optical Coatings
In the multifaceted world of optical coatings, understanding the different types and their specific applications is essential. Optical coatings are not one-size-fits-all; they are carefully engineered to perform specific functions, and their effectiveness depends on the choice of materials and deposition methods. Here, we explore three main types of optical coatings: Anti-Reflective Coatings, High-Reflective Coatings, and Filter Coatings.
Anti-Reflective Coatings are designed to reduce reflections and increase the amount of light transmitted through the optical component. By minimizing reflections, these coatings allow more light to pass through, enhancing visibility and clarity. This type of coating is commonly found in eyeglasses, camera lenses, and display screens, where reducing glare and reflections is crucial for optimal performance.
High-Reflective Coatings, on the other hand, are used to reflect a high percentage of incident light. Unlike anti-reflective coatings, which aim to transmit more light, high-reflective coatings are designed to reflect as much light as possible. This makes them ideal for applications such as mirrors, where maximum reflection is desired. High-reflective coatings are also used in laser technology, where controlling the direction and intensity of light is vital.
Filter Coatings represent a specialized category of optical coatings that selectively transmit light of specific wavelengths. By allowing certain wavelengths to pass through while blocking others, filter coatings can control the spectral characteristics of light. This makes them vital in various applications like photography, where they can enhance color balance, and astronomy, where they can isolate specific spectral lines for analysis.
The development and application of these coatings require a deep understanding of the properties of light and the behavior of materials at the microscopic level. The choice of materials, deposition methods, and design must be carefully tailored to the specific needs of the application. Innovations in materials science and deposition technology continue to expand the possibilities of what can be achieved with optical coatings, enabling new applications and enhancing existing ones.
In conclusion, optical coatings are a diverse and essential aspect of modern optics. Whether reducing reflections for clearer vision, reflecting light for precise control, or selectively transmitting specific wavelengths for specialized applications, these coatings are at the heart of many of the optical technologies we rely on every day. Their continued development and innovation promise to shape the future of optics, enabling new possibilities and enhancing our ability to manipulate and control light in ways that were previously unimaginable.
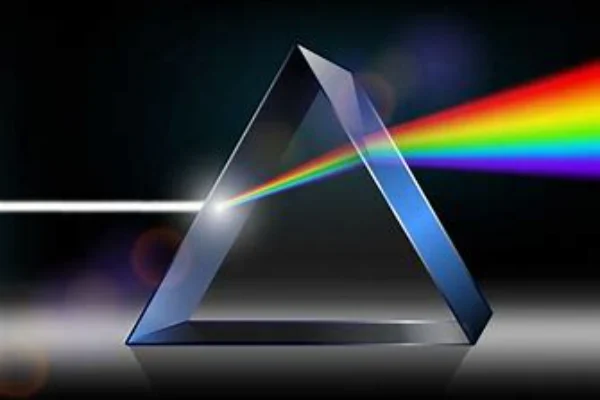
Challenges and Solutions in Thin Film Deposition
Thin film deposition, the process of applying thin layers of material onto a substrate, is at the core of optical coatings. While it has revolutionized the field of optics, it is not without its challenges. Two of the most significant challenges in thin film deposition are achieving uniformity and addressing environmental considerations. Both of these aspects are critical to the success and sustainability of the deposition process, and they require innovative solutions and careful consideration.
Uniformity in thin film deposition is not just a desirable quality; it is crucial. A uniform coating ensures consistent optical properties across the entire surface of the component, leading to predictable and reliable performance. Achieving this uniformity is no small feat. It requires advanced deposition techniques, proper substrate preparation, and meticulous control over the deposition process. The slightest variation in thickness can lead to inconsistencies in the coating’s optical properties, affecting the overall performance of the optical component. Researchers and engineers are continually working on refining deposition techniques and developing new methods to ensure that uniformity is achieved consistently.
Environmental considerations are another significant challenge in thin film deposition. The deposition process often involves the use of chemicals and materials that can be harmful to the environment. Additionally, traditional deposition methods can be energy-intensive, contributing to broader environmental concerns. Recognizing these challenges, the industry is actively working on developing newer methods that are more environmentally responsible. These include reducing waste, minimizing the use of hazardous materials, and adopting energy-efficient practices. The goal is to create a deposition process that not only meets the technical requirements but also aligns with the growing emphasis on sustainability and environmental stewardship.
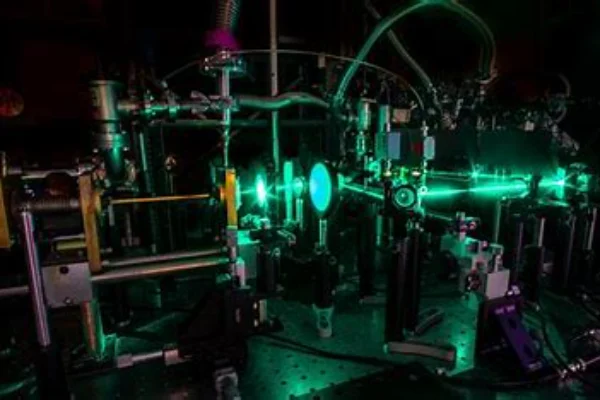
Conclusion: The Future of Optical Coatings
Optical coatings and thin film deposition are integral to modern optics. They offer a wide range of applications and continue to evolve with technological advancements. The future of optical coatings promises even more innovative solutions and applications, making this field an exciting area of ongoing research and development.
FAQs
- What are the main methods of thin film deposition?
- The main methods are Physical Vapor Deposition (PVD) and Chemical Vapor Deposition (CVD).
- How do optical coatings enhance the performance of optical components?
- They control properties like reflection, transmission, and polarization to enhance performance.
- What are filter coatings used for?
- Filter coatings selectively transmit specific wavelengths of light and are used in applications like photography and astronomy.
- Why is uniformity important in thin film deposition?
- Uniformity ensures consistent optical properties across the entire surface of the component.
- Are there any environmental concerns with thin film deposition?
- Yes, but newer methods are being developed to reduce waste and energy consumption, addressing these concerns.
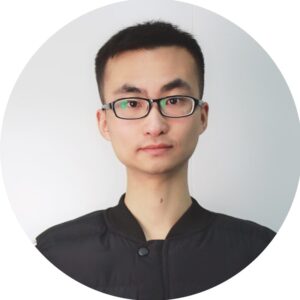
Frank
Frank graduated from the University of Shanghai for Science and Technology, majoring in optics. As a technical engineer at Crylink Company, he deeply understands crystal materials and laser components.
Related Video(s) with this Article
Related Product(s) with this Article
Related Application(s) with this Article